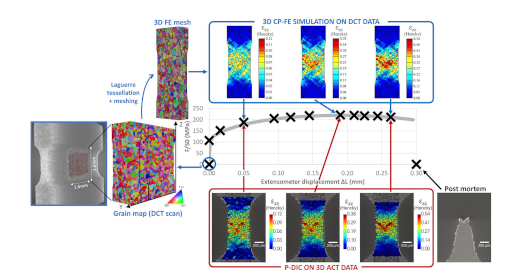
3D strain heterogeneity and fracture studied by in-situ correlative X-ray tomography experiments and CP-FE simulations
To reduce CO2 emissions and improve fuel efficiency, significant effort is put into replacing steel by aluminum alloys in future automotive body panels. In this respect, optimizing the formability of aluminum alloys is key. Since most automotive stamping failures occur near plane strain, an increased understanding of aluminium alloys deformed under plane strain conditions is of particular interest.
With the purpose of investigating the bulk strain heterogeneity and localization and how this affects the final fracture path for an AA6016 T4 specimen deformed in plane strain tension, PhD student Maryse Gille from Centre des Matériaux, Mines Paris visited Xnovo in March 2022 to perform multi-modal, non-destructive X-ray experiments.
First, the microstructure of the undeformed specimen was obtained using lab-based DCT. Absorption contrast tomography (ACT) was then used to measure the natural speckle of intermetallic particles in the material bulk during an in-situ tensile test performed for twelve loading increments up to fracture. Taking advantage of the plane strain condition, the evolution of the internal strain field was determined by two-dimensional digital image correlation (DIC) on the ACT measurements. Finally, crystal plasticity finite element (CP-FE) simulations were performed on the meshed microstructure acquired by DCT and compared with the experimental DIC results.
Correlative tomography and simulations
The experimental strain fields showed early strain heterogeneities in the form of slanted bands, spatially stable over time. The fracture path, determined from the post mortem scan, was found to coincide with the bands exhibiting maximum strain. The measured strain fields are well described by the 3D CP-FE predictions, whilst simulations not taking grain orientations into account were unable to reproduce the measurements. These findings support the hypothesis that crystallographic effects are responsible for early strain heterogeneities, which precede localization and the final failure path. They also promote the use of CP-FE simulations to study the effects of grain orientations on strain heterogeneity, localization and final fracture, for example to optimize aluminium alloy formability.
International Journal of Plasticity
See also
Multimodal investigation of 3D grain structure and local inhomogeneous deformation